In the world of manufacturing and design, the term “press mold” holds significant relevance. But what exactly is a press mold, and why does it matter?
A press mold, also known as compression mold or compression molding, is a manufacturing process used to shape materials such as plastic, rubber, ceramics, and composite materials. It involves the use of a mold cavity, typically made from metal, into which the material is placed. The mold is then subjected to high pressure and heat, causing the material to conform to the shape of the mold cavity and solidify.
This process is widely utilized in various industries for producing a wide range of products, from automotive components and electronic enclosures to kitchenware and consumer goods. The versatility and efficiency of press molding make it a preferred choice for mass production, as it allows for the rapid production of complex shapes with high precision and consistency.
The key components of a press mold include the mold cavity, which defines the final shape of the product, and the press machine, which applies the necessary pressure and temperature to facilitate the molding process. Depending on the material and design requirements, different types of presses, such as hydraulic presses and mechanical presses, may be used.
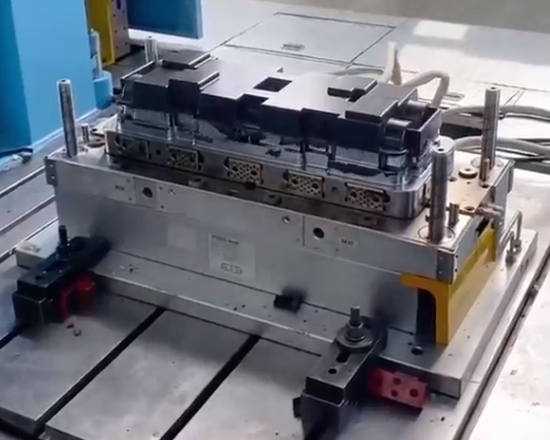
Press molding offers several advantages over other manufacturing processes, including:
- Cost-effectiveness: Press molding enables the production of large quantities of parts at a relatively low cost per unit, making it ideal for mass production.
- High efficiency: The automated nature of press molding results in fast cycle times and high production rates, maximizing efficiency and productivity.
- Design flexibility: Press molds can be customized to produce a wide variety of shapes and sizes, allowing for greater design flexibility and creativity.
- Material versatility: Press molding can accommodate a wide range of materials, including thermoplastics, thermosetting plastics, rubber, and composites, providing versatility in product design and application.
In conclusion, press molding plays a crucial role in modern manufacturing, offering a cost-effective, efficient, and versatile solution for producing a wide range of products. Its widespread use across industries underscores its importance in the world of design and production.
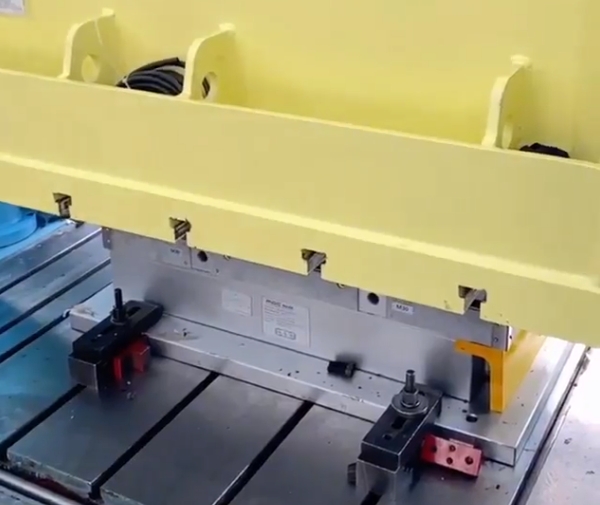