SMC mold (sheet molding compound mold) is a plastic mold that will be filled with resin, The compression mold of reinforcing fiber and filler is prefabricated into a sheet, and then the sheet is heated and formed in a hot mold to make a molded part. SMC molds can play an important role in medical applications, such as:
- Transparent containers: SMC molds can be used to manufacture transparent medical containers, such as test tubes, centrifuge tubes, petri dishes, etc. These vessels have high transparency and optical performance, which can help doctors observe processes such as cell culture, drug response and virus detection. In the manufacturing process, SMC molds can achieve different shapes and sizes through a variety of molding processes, such as stamping molding, injection molding, etc., and can achieve different optical properties through surface treatment, such as polishing, optical coating, etc.
- Operating bed: The operating bed is another important application field. The shell and base of the operating bed need to have high strength and rigidity to ensure the stability and safety of the operating bed. SMC molds can realize complex shapes and structures through mold design and molding process, and at the same time, fillers and fiber reinforcements can be added to improve strength and rigidity.
- Hospital beds and wheelchairs: Hospital beds and wheelchairs are also important applications of SMC molds in medicine. The shells and bases of these devices need to be high-strength and lightweight, so that patients and medical staff can move and transport. SMC molds can achieve different shapes and sizes through a variety of molding processes, and fillers and fiber reinforcements can be added to improve strength and lightweight properties.
- Diagnostic equipment: SMC molds can be used to manufacture shells and structural components of medical diagnostic equipment, such as X-ray machines, CT machines, nuclear magnetic resonance machines, etc. These devices need to have high precision and stability to ensure diagnostic accuracy and safety. SMC molds can realize complex shapes and structures through mold design and molding process, and at the same time, fillers and fiber reinforcements can be added to improve strength and stability. In addition, the surface quality of SMC molds is also very important, and different surface finishes and optical properties can be achieved through a variety of surface treatment technologies, such as grinding, painting, etc.
- Others: The medical device shell made of SMC mold has a smooth surface, easy to clean, and has high strength and rigidity, which can ensure the stability and safety of the device. The handles and housings of surgical instruments can also be made of SMC molds, which have high strength, rigidity and corrosion resistance, and at the same time have smooth surfaces, which are easy to clean and sterilize. The housing and base of dental equipment can be made of SMC molds, which have high strength and rigidity, and at the same time have a smooth surface, which is easy to clean and disinfect. The housing and structural parts of medical imaging equipment can be made of SMC molds, which have high precision and stability, and at the same time have a smooth surface, which is conducive to optical imaging.
In general, SMC molds can be used to manufacture various parts of medical equipment. The advantages are that the material has the characteristics of high strength, corrosion resistance, high temperature resistance, etc., as well as good formability and surface quality, as well as good optical properties, and It is also beneficial to the weight reduction of medical equipment and the reduction of manufacturing cost.
MDC Mould is a well-known mold manufacturer at home and abroad. The picture below is the MRI machine Shell Mold made by MDC Mould. The molds developed by our company have the advantages of high difficulty, long life, short cycle time, reasonable price, prompt delivery and considerate service, especially in the field of SMC molds, which are favored by customers at home and abroad. If you have any needs, welcome to contact us.
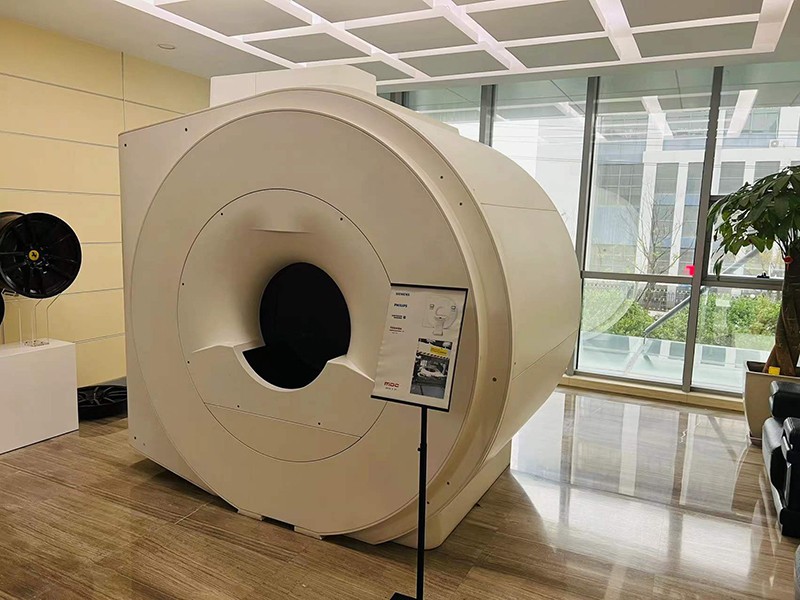