The revolution of carbon fiber in the aerospace industry traces back to the 1960s when this innovative synthetic material was introduced in the assembly of Rolls-Royce jet engine fan blades. Since then, the demand for carbon fiber in both private and commercial aircraft has surged, owing to the advantages it offers to the industry.
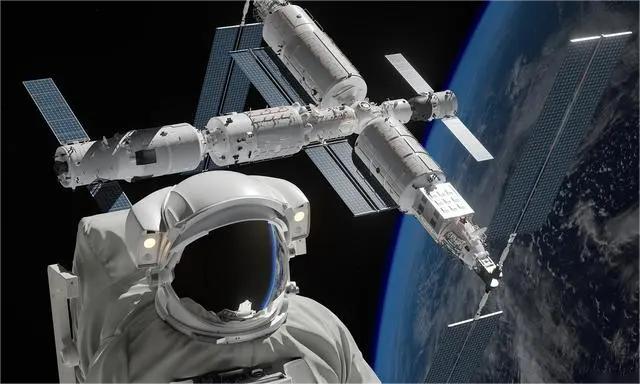
What is Carbon Fiber?
Carbon fiber is a synthetic material initially developed in the late 1800s. It consists of woven fibers—finer than human hair—carbonized and reinforced with resin, resulting in an incredibly strong and durable material. Carbon fiber products are shaped by laying the material onto molds, allowing for seemingly endless shapes to be formed.
Applications in Aerospace
Modern aircraft increasingly utilize carbon fiber in the manufacturing of fuselages, wings, engine components, and more. But what sparked the revolution in the aerospace industry and why?
Strength and Corrosion Resistance
Carbon fiber offers higher strength-to-weight ratio compared to aluminum. Its strength enhances durability, crucial for withstanding forces like wind resistance during flight. Moreover, being chemically stable, carbon fiber resists corrosion—a significant advantage over aluminum, prone to corrosion.
Fuel Efficiency
One of the key factors in aircraft fuel efficiency is weight reduction. Carbon fiber, being approximately 40% lighter than aluminum, significantly reduces the aircraft’s weight, leading to lower fuel consumption and costs. This factor marks a significant step forward in reducing carbon footprint and embracing eco-friendly practices.
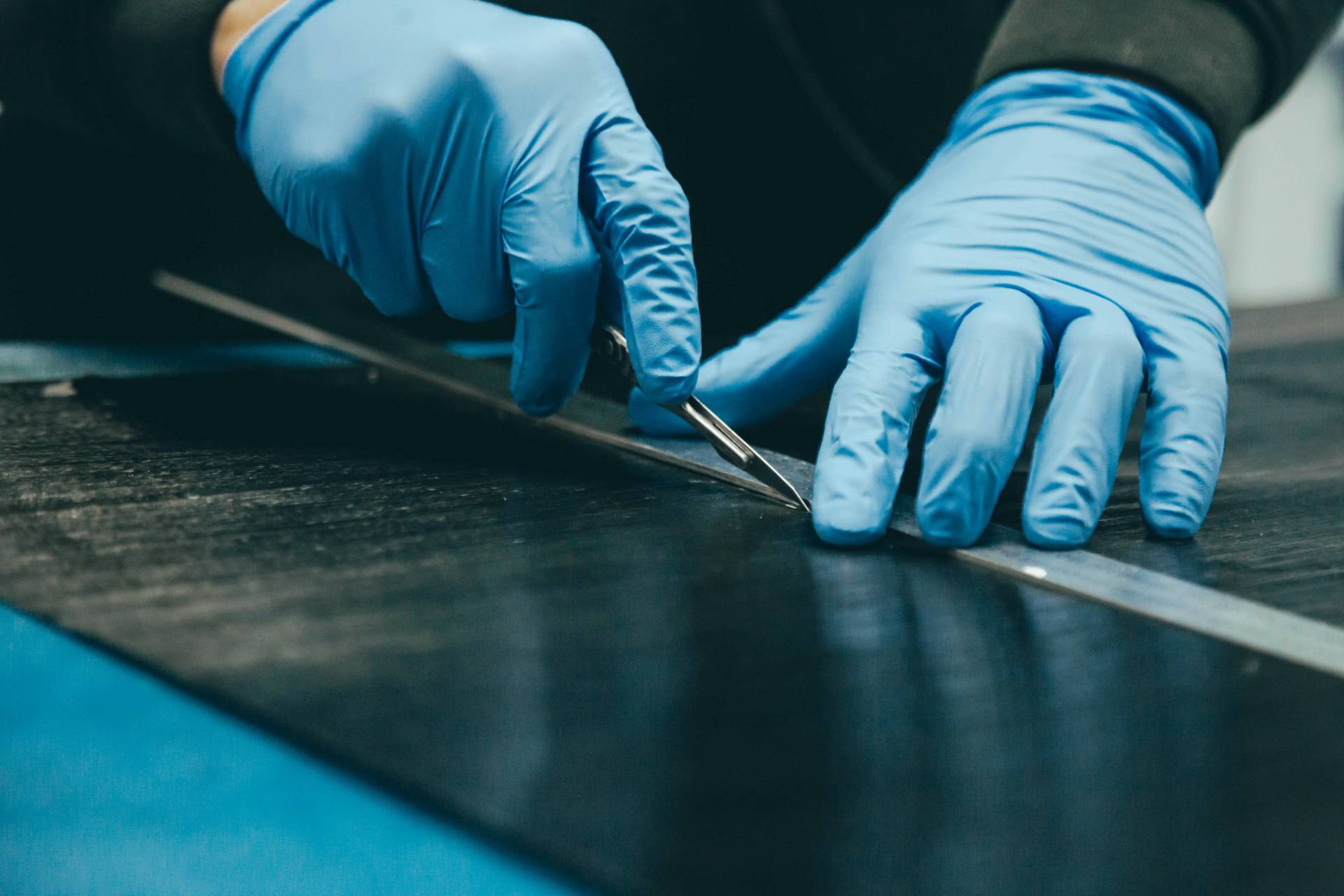
Easier Manufacturing
Advancements in carbon fiber design and manufacturing have made production more accessible. Despite being a complex process, improvements in research and manufacturing techniques have led to increased production levels, making the material more accessible to aerospace manufacturers. Molded into almost any shape, carbon fiber integration reduces part count and assembly time, further lowering manufacturing costs.
Enhanced Aerodynamics
Carbon fiber’s design, stiffness, and smoothness contribute to improved aerodynamics, reducing drag and enhancing aircraft performance. Its usage in major structures such as wings aids in better aerodynamic performance, leading to improved fuel efficiency and reduced fuel costs.
In conclusion, carbon fiber stands as a revolutionary material in the aerospace industry, offering unmatched strength, durability, and versatility. Its widespread adoption signifies a paradigm shift towards more efficient, environmentally conscious aviation practices.