Composite molding exterior refers to the manufacturing of durable, lightweight, and aesthetically advanced exterior parts using compression molding technologies. These components are made from high-strength materials such as SMC (Sheet Molding Compound), BMC (Bulk Molding Compound), and carbon fiber-reinforced polymers. They are widely used in the automotive industry, architectural panels, commercial transportation, and outdoor infrastructure.
Why Choose Composite Molding for Exterior Applications?
Composite molding offers superior performance over traditional materials such as metal and plastic in demanding exterior environments. Key advantages include:
- Weather Resistance: Excellent durability against UV, rain, heat, and frost.
- Lightweight & Strong: Ideal for reducing structural load while maintaining strength.
- Design Flexibility: Molds allow for complex shapes, textures, and surface finishes.
- Corrosion-Free: Unlike metals, composites do not rust or corrode.
- Sustainability: Recyclable materials and energy-efficient production processes.
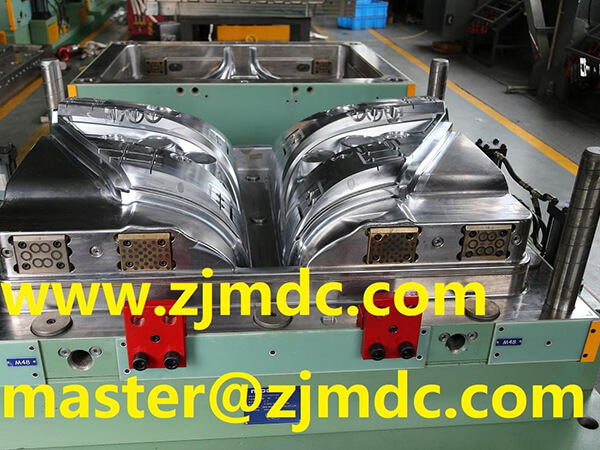
Core Composite Molding Technologies
SMC Molding
SMC is a fiberglass-reinforced polyester material widely used for large-scale exterior parts. Common SMC exterior molds include automotive bumper molds, truck exterior panel molds, and antenna cover molds. It supports high-volume production with excellent repeatability and precision.
BMC Molding
BMC offers excellent dielectric properties, making it suitable for electrical enclosures and junction box covers exposed to outdoor conditions. BMC molds ensure tight tolerances and reliable structural integrity.
Carbon Fiber Molding
Carbon fiber molding is applied to high-performance sectors such as motorsports and aerospace. For exterior use, it provides unmatched strength-to-weight ratio and a sleek appearance, commonly used in racing car body kits, mirror housings, and hoods.
Typical Applications
- Automotive: Bumper covers, tailgates, side skirts, mirror covers, wheel arches
- Commercial Vehicles: Truck fairings, rear guards, cab exteriors
- Architecture: Decorative façade panels, soffits, eaves, outdoor signage
- Infrastructure: Antenna housings, distribution box covers, smart city terminals
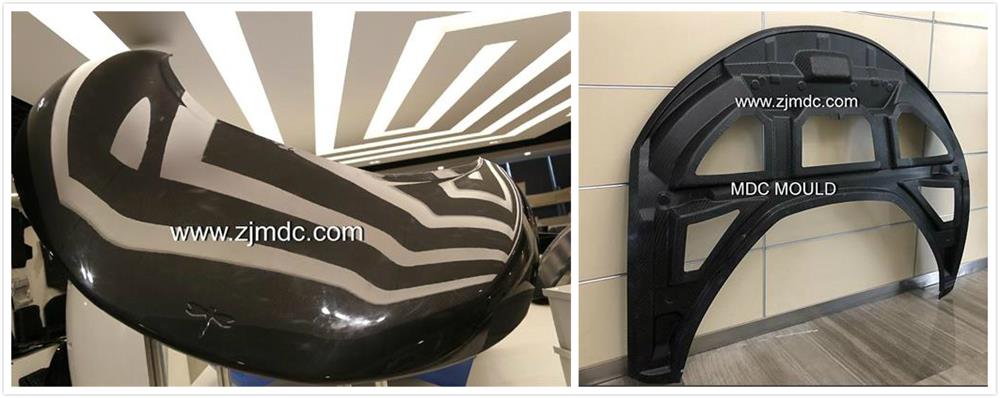
Precision Molds for Composite Exterior Parts
High-quality molds are crucial to the success of composite exterior molding. At MDC Mould, we provide expert tooling for:
- SMC bumper molds
- SMC truck panel molds
- Carbon fiber car body molds
- Composite antenna housing molds
- BMC distribution box molds
Conclusion
Composite molding exterior solutions are revolutionizing the way exterior components are produced and used across industries. Their performance, versatility, and sustainability make them a smart choice for next-generation design and manufacturing.
Whether you need custom SMC exterior molds, carbon fiber tooling, or composite molding solutions, we’re here to help you turn your concept into high-precision products.